Philips moet 7 miljoen Senseos bij consumenten terughalen. Geschatte kosten: 30 mln. Brand in het magazijn, wanprestaties van leveranciers, product recalls, capaciteitsproblemen in transport, problemen met ICT, stroomstoringen, een falend nieuwe ERP-systeem of natuurgeweld kunnen grote gevolgen hebben. In een economie waarin alles met elkaar is verbonden, verspreiden verstoringen zich razendsnel door het hele logistieke netwerk en staat de goederenstroom plotseling stil. Het kost geld om die goederenstroom weer op gang te helpen en klanten krijgen tijdelijk geen producten. De gevolgen op langere termijn zijn groot; imagoverlies, verloren klanten of zelfs faillissement. Dit artikel leert u de lessen van ondernemingen die grote verstoringen hebben meegemaakt? Wat kunt u nú doen om ellende later te voorkomen?
- Ondernemen is risico’s nemen
- Gebrekkig risicobewustzijn leidt tot achterstand
- Onderken de risico’s in de gehele keten
- Een goede relatie met partners èn concurrenten betaalt zich terug
- We organiseren onze eigen verstoringen...
- Concrete doelstellingen...
- Liever bekwame mensen dan dikke draaiboeken
- Aanpak in de praktijk
- Tenslotte
Ondernemen is risico’s nemen
Door de toegenomen globalisering en uitbesteding, vaak naar verre regio’s, zijn logistieke ketens in de afgelopen jaren geëvolueerd naar complexe wereldwijde logistieke netwerken. Een verstoring in een deel van een logistieke keten verspreidt zich razendsnel door het hele netwerk. Organisaties die gestructureerd risico’s wegen, prioriteiten stellen en maatregelen nemen, behalen daarmee voordelen; risicomanagement en logistiek loont. Ondernemingen maken hun logistieke processen ‘resilient’. Resilience is de veerkracht waarmee ondernemingen of logistieke ketens herstellen van ernstige verstoringen en vervolgens weer hun afspraken met klanten kunnen nakomen.
Product recall Aardappelkroketjes en -bolletjes, die tijdens het frituren exploderen, melkpoeder met de giftige stof melamine, een ondeugdelijke boormachine, loodhoudende verf op kinderspeelgoed en exploderende Senseos. Ineens moet u uw producten uit de winkels, of misschien zelfs bij consumenten, terughalen. In 2008 was het aantal recalls van en waarschuwingen voor voedingsmiddelen groter dan ooit, volgens de voedsel- en waren autoriteit.Bij een recall krijgt u te maken met onverwachte kosten. Zo zijn er de kosten van onderzoeken, van het terughalen en het vernietigen van de producten. Tel daarbij op de advertenties om de consument op de hoogte te stellen van de terughaalactie. Bij een levensmiddel dat schadelijk kan zijn voor de gezondheid moet een advertentie met een publiekswaarschuwing worden geplaatst in minimaal twee landelijke dagbladen. Door alle negatieve media-aandacht kan uw imago worden geschaad. Het kan uiteindelijk zelfs de continuïteit van uw onderneming in gevaar brengen. Een logistiek risico om echt serieus te nemen dus.Het start met een goed plan. Maak een plan voordat u een probleem krijgt. Beslis wanneer u actie moet ondernemen en schat het risico in. Als een recall actie nodig is: wat gaat u dan doen? En wat gaat u doen als het gaat om producten die al bij de consument zijn? Na de corrigerende actie; wat heeft u geleerd van de ervaringen? Een recall is vaak niet gedekt door een aansprakelijkheidsverzekering waardoor u zelf voor de kosten opdraait. Hoe gaat u dan de kosten opvangen? Of gaat dit u niet overkomen? |
Ernstige verstoringen komen misschien niet vaak voor, maar kunnen wel grote financiële schade opleveren. Risico’s komen voor aan de aanbod- en vraagzijde en binnen de onderneming zijn er proces- en controlerisico’s.
Risico’s verschillen per sector. In een sector waar de capaciteit maximaal benut wordt, is bijvoorbeeld minder speelruimte om verstoringen op te vangen. Andere sectorspecifieke zaken: mate van concurrentie, voedselveiligheid, kans op stakingen, afhankelijkheid van stroomvoorziening, brandbaarheid of diefstalgevoeligheid van de producten. De leveringsproblemen met radioactieve isotopen na onderhoudsproblemen bij vier van de zes fabrieken wereldwijd leidde tot problemen in ziekenhuizen. Ineens is er een tekort, doordat er geen rek zit in de productiecapaciteit. Een probleem dat de hele sector treft.
Figuur 1 Risico’s in logistiek
Op korte termijn betekent dit enorme kosten, slechte prestaties en ontevreden klanten. Op middellange en lange termijn heeft de onderneming omzet- en winstverlies, en wellicht een imagoprobleem. Of stevent zelfs af op een faillissement. Uit onderzoek blijkt dat twee jaar na de ramp nog steeds significant minder winst wordt gemaakt door de getroffen ondernemingen.
Het blijkt in de praktijk vaak niet bekend wat achteraf eigenlijk precies de schade is geweest van een verstoring. Men heeft de schade in euro’s niet paraat. Er zijn kosten die niet op een factuur vermeld staan, maar die wel ten koste gaan van het bedrijfsresultaat. Zoals klantverlies of de managementtijd die het kost om claims te bespreken en de ellende af te handelen. Noodsituaties brengen daarnaast soms ook nog andere problemen boven water die normaal gesproken geen echt breekpunt zijn.
Gebrekkig risicobewustzijn leidt tot achterstand
Er wordt weinig nagedacht over risico’s in logistieke ketens. Tijdens een workshop van TNO over risicomanagement, zei een van de managers bij een logistieke dienstverlener: ‘‘Je mag het eigenlijk niet zeggen, maar eigenlijk zou ieder bedrijf een kleine verstoring moeten meemaken. Zonder dat dit echt tot ernstige gevolgen leidt, maar wel nét erg genoeg om mensen bewust te maken van het nut om te anticiperen op crises.’ Hij had gelijk. Steeds weer blijkt dat ondernemingen die er bewust mee bezig zijn het òf moeten van de wetgever of een klant, òf zelf een vervelende verstoringen mee hebben gemaakt. Het besef komt vaak door concrete ervaringen in de praktijk; ‘Een slim iemand leert van zijn fouten, een slimmer iemand leert van andermans fouten’.
En ineens valt de leverancier weg Nokia troefde Sony Ericsson af door betere alertheid op de gevolgen van verstoringen. De semiconductorfabriek van Philips in de Verenigde Staten werd in maart 2000 door een lichte brand getroffen. Philips informeerde de klanten Nokia en Sony Ericsson over de omstandigheden, maar alleen Nokia realiseerde zich de impact op haar logistieke keten. De leveringen vanuit Philips werden dan ook extra kritisch bekeken, en toen bleek dat de verstoring groter was dan verwacht, trok Nokia de noodplannen uit de kast. Nokia eiste van Philips dat alle beschikbare restcapaciteit aan Nokia werd toegewezen en kon daardoor beter voldoen aan de marktvraag. Sony Ericsson daarentegen ondernam geen actie en wachtte af. Het gevolg was dat Ericsson tijdelijk minder mobieltjes kon leveren, waardoor Nokia zijn marktaandeel op Sony Ericsson kon vergroten. |
Onderken de risico’s in de gehele keten
U kent uw leveranciers en hopelijk ook uw klanten, maar weet u wie de leveranciers van uw leveranciers zijn of de klanten van uw klanten? De directe relaties kennen we meestal, maar de kwaliteit van een ketenprestatie wordt soms net zo hard bepaald door de indirecte relaties. Als uw leverancier de eigen processen goed in de hand heeft, maar zijn belangrijkste toeleverancier gaat failliet, dan wordt hij meegezogen in de problemen. En u dus ook.
Een goede relatie met partners èn concurrenten betaalt zich terug
Grote verstoringen hebben effect op meerdere plekken in de keten. Dat betekent ook dat u meerdere partijen nodig hebt om de gevolgen te beperken. In verschillende sectoren is het zelfs gebruikelijk dat concurrenten elkaar helpen in tijden van nood. In het magazijn van de logistieke dienstverlener van Cargill Cocoa in de Zaanstreek ontstond in juli 2003 brand. Sommige klanten schakelden - in overleg met Cargill - tijdelijk over op de concurrent om out-of-stocksituaties te voorkomen. Dit laatste was relatief gemakkelijk, omdat weinig klanten van Cargill Cocoa met single sourcing werkten. De concurrent heeft echter geen misbruik gemaakt van de situatie vanuit het besef dat het de volgende keer wel eens andersom zou kunnen zijn.
We organiseren onze eigen verstoringen...
In een economie waarin alles met elkaar is verbonden, verspreiden verstoringen zich razendsnel door het hele logistieke netwerk van een organisatie. Door die verstoringen komt de goederenstroom tot stilstand. Het kost geld om die goederenstroom weer op gang te helpen en klanten krijgen tijdelijk geen producten. Verstoringen worden steeds vaker veroorzaakt door bedrijfs- of keteninterne risico’s voortvloeiend uit vooral het streven naar meer efficiency en uitbesteding van logistieke processen aan andere ondernemingen wereldwijd. De verstoringen worden minder vaak veroorzaakt door externe invloeden zoals politieke onrust of natuurgeweld. U kunt – nee, sterker nog: u moet – er dus zelf wat aan doen.
Concrete doelstellingen...
Bij veel risicomanagementprojecten is het doel dat er minder risico moet worden gelopen, maar hoeveel? Wellicht helpt het als men eerst kwantificeert wat de organisatie moet blijven kunnen doen in geval van nood. Dat is moeilijk, maar helpt bij het stellen van prioriteiten bij de inzet van capaciteit en middelen. Veel organisaties hebben – door het ontbreken van een doel - grote moeite om te bepalen waarin ze wel of niet moeten investeren bij risicomanagement.
Bij Defensie moet de snelle interventiemacht binnen vijf dagen ingezet kunnen worden in crisisgebieden over de hele wereld en het daar als relatief kleine, maar goed getrainde en geoutilleerde groep, circa dertig dagen uithouden. Dit is een specifieke doelstelling.
De les voor het bedrijfsleven is dat onderscheid nodig is naar type klanten en bijbehorende service ten tijde van een ramp. Wat wil je voor wie betekenen tijdens een crisis? Wilt u de key accounts het eerst helpen, of de klanten waar u de meeste marge op maakt? Hoe snel moeten ze dan weer goederen krijgen? En welke klanten houden zelf een buffervoorraad aan? Hoe moet u het dus organiseren?
Liever bekwame mensen dan dikke draaiboeken
Natuurlijk moeten procedures worden vastgelegd op papier. En natuurlijk helpt het ook wel om dingen op te schrijven. Maar bij een crisis gaat het er vooral om dat de verantwoordelijke managers snel en doortastend handelen om mensen, gebouwen, materieel, goederen, geld en informatie veilig te stellen. Daarom is het zinvol om uw mensen te trainen in het doordenken van gevolgen van rampen, en in een groep te bespreken hoe u dit zou aanpakken. Managers dienen elkaar dan wel kritisch te bevragen (‘maar hoe ga je dat dan organiseren?’).
De grote dag bij Technische Unie De directeur Logistiek van groothandel Technische Unie verraste zijn logistieke management team op maandag 11 februari 2008. Het leek een gewoon tweewekelijks vergaderdagje te worden. Maar, een televisie stond aan. De nieuwslezer vertelde over een uitslaande brand in het distributiecentrum van Technische Unie. Het managementteam kreeg de opdracht om de persconferentie voor te bereiden. De rest van de dag werd besteed aan allerlei vragen. Hoe om te gaan met de acute crisissituatie? Hoe kunnen we ervoor zorgen dat we zo snel mogelijk weer back-in-business zijn? Gaan we alles weer precies zo opbouwen als het was, of voeren we meteen de nodige veranderingen door? Zo werd gewerkt aan bewustwording en werd vaardigheid geoefend. |
Aanpak in de praktijk
Hoe vergroot u nu uw eigen ‘voortzettingsvermogen’? TNO ontwikkelde een stappenplan met vijf bouwstenen.
Stap 1: Bereidt u voor en breng focus aan
Werk aan de bewustwording binnen uw bedrijf, en vergeet niet om focus aan te brengen. Als u te weinig aandacht besteedt aan afbakening van het project, houdt u daar last van in alle volgende stappen; waarom willen we het? Wat vinden klanten ervan? Stel een risicoteam samen!
Stap 2: Breng strategie en processen in kaart
Is die stap nodig? De strategie en processen zijn toch bij iedereen bekend? Misschien soms wel, maar heel vaak ook niet. En als de strategie bekend is, bestaat de kans dat de top van de organisatie al nadenkt over het aanpassen van de strategie aan marktwensen. Aangezien u bezig bent met de toekomstbestendigheid van de organisatie, moet u de laatste stand van zaken kennen.
Stap 3: voer een FMEA uit
Een failure mode and effect analysis (FMEA) is een methode om op een gestructureerde manier de mogelijke faalwijzen in kaart te brengen, deze te waarderen en te ordenen. Met een FMEA kan op voorhand in kaart gebracht worden wat de gevolgen kunnen zijn van een mogelijk falen, om vervolgens constructiemaatregelen (zoals in de automobielindustrie) of procesmaatregelen (zoals bij logistieke processen) te nemen. Hiermee kunnen vervolgens de gevolgen worden verminderd of voorkomen. U brainstormt over risicosoorten, over de kans dat het fout gaat en over de gevolgen op basis van de FMEA. Organiseer in deze stap enkele workshops, en bouw ook tijd in ter bezinning. Dit betekent dat mensen alsnog na de eerste workshop met nieuwe inzichten kunnen komen, of zelfs dat mensen op onderzoek uit gaan en nieuwe risico’s vinden.
Figuur 2 FMEA
Stap 4: Bepaal de resilience strategie en pas logistiek concept aan
Bedenk welke ingrediënten u wilt inzetten om de resilience strategie te bepalen. U kunt de kwetsbaarheid reduceren door:
- meer overvloed in te bouwen, bijvoorbeeld door extra voorraad van knelpuntproducten, back-up servers (op een andere locatie) om gegevens veilig te stellen, noodaggregaten voor stroomvoorziening of extra personeel op afroep;
- meer flexibiliteit in te bouwen, bijvoorbeeld door te kunnen switchen tussen leveranciers, producten modulair te ontwerpen, via verschillende transportketens uw klant te bedienen of uw afhankelijkheid van één grote klant te verminderen;
- meer transparantie te creëren, zoals het direct volgen van zendingen in de keten en van marktontwikkelingen of het delen van informatie met partners;
- meer samen te werken in de keten, bijvoorbeeld door samen met klanten, leveranciers of dienstverleners te anticiperen op verstoringen. En om samen met hen de ellende te beperken als het zover is.
Stap 5: Volg het op: plan, do, check, act
Maak een plan, betrek uw mensen en stem dit af met klanten en leveranciers. Volg het op, borg en herhaal deze cyclus periodiek: de organisatie en haar omgeving veranderen continue. Dit betekent dat risico’s mee veranderen.
Tenslotte
De wereld verandert en daarom passen we ons aan. De meeste trends leiden er toe dat de risico's in de wereldwijd logistieke ketens alleen maar verder toenemen. De kleinste verstoring kan de gehele logistiek keten lam leggen. Aberdeen Group heeft onlangs onderzocht dat 99 procent van de ondernemingen een verstoring heeft gehad, 58 procent van de ondernemingen daarvan financiële gevolgen ervaren, maar dat slechts 12 procent van de bedrijven zich daarop echt heeft voorbereid.
Managers moeten actie nemen om de logistiek op langere termijn robuust te maken en te houden. Toch zijn klanten en aandeelhouders eerder geneigd naar de wat kortere termijn te kijken. Het managen van risico vraagt nu eenmaal ook om strategieën die anticiperen op vervelende voorvallen die, als al ooit, maar eens in de paar jaar voorkomen en bovendien grote investeringen met zich meenemen.
Om ervoor te zorgen dat een bedrijf door kan blijven produceren, distribueren en verkopen na een verstoring in de logistieke keten, is het belangrijk dat de logistieke keten resilient is; je moet ervoor dat zorgen dat je de schade na verstoringen beperkt en snel weer terugkeert naar de gewenste situatie.
Het is dus nodig de risico's van verstoringen in de logistieke keten te onderkennen en u daarop voor te bereiden. Veel bedrijven hebben noodplannen, maar die zijn bijna altijd bedoeld om mensen in veiligheid te brengen of milieuschade te voorkomen. Maar een ernstige verstoring in de logistieke keten, betekent ook dat leveringen haperen. Plannen mag niet ontbreken voor het op gang krijgen van de goederenstroom - en niet te vergeten de informatiestroom die deze goederenstroom moet aansturen. Vroeg of laat gaan er dingen mis. Als u hierop anticipeert in plaats van afwacht, bent u duidelijk in het voordeel. Pro-actief dus.
Dit artikel is gebaseerd op ‘Risicomanagement en logistiek, kan uw organisatie tegen een stootje’ van Bart Lammers, Walther Ploos van Amstel en Pascal Eijkelenbergh.
(Uitgeverij Pearson in samenwerking met TNO Mobiliteit en Logistiek)
Gerelateerde artikelen
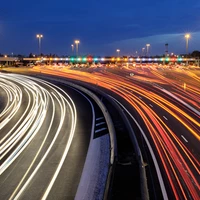
Eén snelheid op de snelweg
ReindeR Rustema
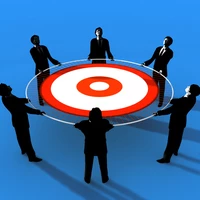
Waarom werkt risicomanagement niet?
Actueel MNGMNTST
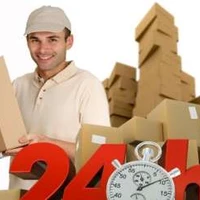
Hoe win je de Nederlandse logistiekprijs
Walther Ploos van Amstel
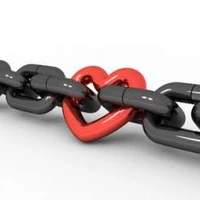
Deel uw ervaringen op ManagementSite
Wij zijn altijd op zoek naar ervaringen uit de praktijk, wat werkt wel, wat niet.
SCHRIJF MEE >>
Als u 3 of meer artikelen per jaar schrijft, ontvangt u een gratis pro-abonnement twv €200,--
Een risico is volgens mij (ook volgens de auteurs trouwens) gedefinieerd als een combinatie van de kans dat een misser optreedt en de ernst van de gevolgen ervan. Maar al weer gaat het in dit artikel alleen om het voorbereid zijn op, en het aanpakken en minimaliseren van, de ernst van de gevolgen. Zou het niet beter zijn beleid en planning naast beperking van de ernst veel meer te richten op het beperken van de kans, op het voorkomen van het optreden van het probleem. Dat betekent dat de vraag gesteld wordt naar de waarschijnlijke oorzaken van de misser en het treffen van maatregelen tegen het optreden daarvan.
Voorkomen is toch beter dan genezen? Merkwaardig dat dit bij risico management geen prominente (soms zelfs géén) plaats krijgt. Risico management behoort volgens mij te bestaan uit het verkleinen van de kans dàt iets mis gaat én verkleinen van de ernst àls iets mis gaat. En niet alleen het laatste!
Goed stuk, graag maak ik gebruik van jullie heldere plaatje over risico-management / risico's in logistiek. De rol van stakeholders zou overigens nog wel iets beter naar voren komen door een externe omgeving en stakeholder schil te tekenen. dan past de scenariomethode ook mooi in het plaatje, een zeer bruikbare methode voor risico-management. Verder ben ik blij dat de FMEA methode (afkomstig uit de productiesector, autoproductie), eindelijk (!) tot het hogere managementniveau aan het doordringen is als een bijzonder geschikte methodiek voor risico-analyse / management. Niet alleen in de logistieke sector overigens.
Maarrrrr, jullie geven hier echter het verkeerde voorbeeld van toepassing van FMEA (ook wel: FMECA). FMEA kan je alleen gebruiken als je een goede database van (ver)storingen en gevolgen daarvan hebt. Als dat er niet is, of van onvoldoende betrouwbaarheid en volledigheid, zoals in jullie voorbeeld, kan je beter een techniek als FTA (Fault Tree Analysis) gebruiken.
Iets anders waar ik ook al heel lang niet blij van wordt is de Deming cirkel: Plan - Do - Check -Act. Groot gemis hierin een eerste fase: Onderzoek & ontwerp (O&O). Beleid en strategie verdient een goed (voor)onderzoek en ontwerpproces. Daarna maak je pas een plan, doe je .... In de Deming cirkel is hier dus geen plaats voor. De Deming cirkel is leuk voor vaststaande /standaard processen waar alleen nog een verbeterproces bij in werking is. Wanneer je breder en innovatiever wil kijken verwordt de Deming cirkel tot een 'zinloze' "hond bijt in eigen staart" routine.
Het zou fijn zijn als consultants bedrijven hier eens over gaan voorlichten.
Groet en dank voor jullie ontwikkelingswerk om de FMEA techniek in risicomanagement te populariseren.
Succes!
Nico Janssen
Nico schrijft helemaal terecht dat dit soort instrumentarium niet toereikend is bij strategische bedrijfsontwikkeling.
Mischien mag ik hier verwijzen naar mijn artikel op digitaalbestuur.nl over het verschil tussen veranderen en verbeteren. Daar beschrijf ik het gehele proces op een hoger aggregatieniveau.
De klassieke strategische Ist-Soll combinatie worden daar uitgebreid met een Wird en Bleibt fase. Zie voor meer informatie ook http://viavertex.org
Zie voor het artikel; http://digitaalbestuur.nl/opinie/structureer-verandering